Turboexpanders
Gas and Process turboexpanders are offered in compressor-loaded & Generator-loaded configurations to supply specific applications.
Flow Control :
The expander variable nozzle guide vanes are designed to provide zero blow-by, positive actuation and high efficiency over a broad operating range. This is often accomplished by using proprietary or patented mechanisms incorporating a pressure actuated sealing ring. This design eliminates side leakage and prevents nozzle galling. The mechanism should be designed to withstand full expander inlet pressure and can often be varied from approximately zero to 130% of the design flow through the machine.
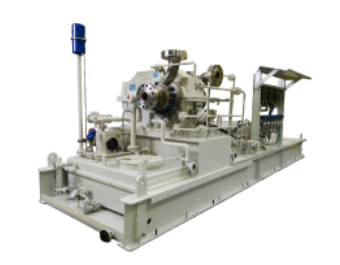
Classification of Turboexpanders:
Suction pressure (max.)
70 Bar
Discharge pressure (max.)
20 Bar
Suction temperature
- 60 to +200Cº
Inlet-flow range
3500 to 400,000 M3/h
Power Range
75kW to 5MW
Gases handled
Air & All Process Gases
Bearing Systems:
- Oil Bearings
We offer horizontally-split, high-speed pinion bearings featuring five self-centering pads that ensure stable rotation. Horizontally-split bearings are especially easy to inspect and maintain. Tilting-pad bearings, which are used on high-speed shafts, and sleeve bearings, used on low-speed shafts, ensure reliable performance, efficiency, and optimal speeds for each process.
- Active Magnetic Bearings Development
We also offer designs using active magnetic bearings. Active Magnetic Bearings generate a magnetic field to align the shaft in its centerline. This eliminates friction and the need of lubrication. The electromagnets of Active Magnetic Bearings are controlled with rotor position sensors by a digital control cabinet. The result which is a combination of lower maintenance, higher reliability, and increased durability boosts equipment performance.
- International Standards
Using the latest CAD technology, customized packaged sets are designed to comply with the requirements of international standards such as API, ASME and AGMA.
Tests:
- All produced expanders are tested as per ASME PTC 10 standard;
- According to API standard, Bright Internacional is able to perform mechanical experiments for single stage or multistage IGCs in order to balance, predict vibration and safety of the system; Furthermore, according to ASME PTC10 standard, performance tests are done to ensure the performance of each single product;
- Impellers balance and vibration levels are very important which ignoring them can cause catastrophic failures in the field. We conduct various tests to address these critical issues;
- Impellers are dynamically balanced to ISO G6.3 minimum;
- Full-speed, mechanical run test is performed on the compressor assembly;
- Vibration analysis conducted at operating speed;
- In-depth bearing analysis designed to detect any potential bearing problems.